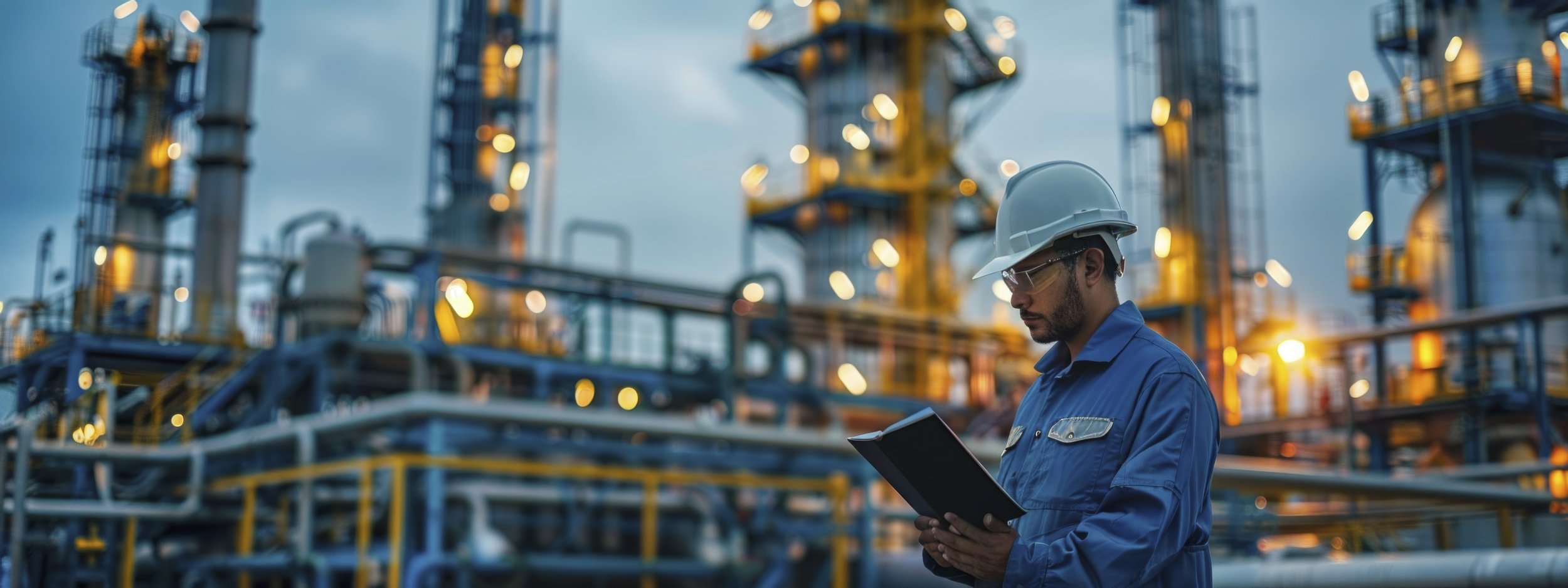
Our Services
Looking to strengthen your hazardous area compliance and safety strategy?
Book a consultation with Mantl-Ex today. We take the time to understand your unique operational challenges and provide expert, third-party guidance to help you stay compliant, reduce risk, and achieve peace of mind in hazardous environments.
ATEX & IECEx Inspections
At Mantl-Ex, we carry out three main grades of hazardous area inspections as per the IEC 60079-17 standard: visual, close, and detailed inspections. Each one has its place depending on the type of equipment, the environment, and how long it’s been since the last check. We're not just there to tick off a list, we're there to really understand what's happening on your site, how your Ex equipment is aging, and whether your compliance is holding up under real-world conditions.
Visual inspections are the starting point — no tools, no opening covers, just trained eyes picking up on obvious faults. Things like damaged enclosures, missing bolts, incorrect equipment in the wrong zone, or anything clearly non-compliant. It’s quick but still critical. A visual inspection can tell us a lot about how well a site is being maintained or where deeper issues might be hiding.
Then there’s the close inspection, which goes a level deeper. We’ll get up close, most likely with a torch and a mirror, but still without opening anything up, or equipment isolation. We’re looking for issues that might not be obvious at a glance — signs of corrosion, loose fixings, deteriorating seals, and improper earthing. It’s about catching the stuff that’s starting to go wrong before it turns into a bigger problem.
Finally, we have the detailed inspection, and this is where we get hands-on. Covers come off, terminals get checked, torque settings verified, this requires equipment isolation. It's a full physical inspection of the internal and external condition of the Ex equipment. This is compulsory for new installations or after authorised modifications, but it’s also part of periodic maintenance for high-risk equipment or older areas. A detailed inspection gives you the full picture, and it’s where experience really matters. Not just knowing the standards, but understanding what failure looks like in the real world.
All of these inspections tie back to the Equipment Protection Level (EPL) and Zone classification — Zone 0, Zone 1, or Zone 2 — and we apply the inspection type according to risk. For example, equipment in Zone 0 (where an explosive atmosphere is present continuously or for long periods) is going to need more rigorous attention than Zone 2, where it’s only likely to occur in abnormal conditions. We don’t believe in over-inspecting to pad out a report, but we also don’t cut corners. We strike the balance between regulatory compliance, operational safety, and cost efficiency.
Whether it’s a new installation or part of your routine maintenance program, we’ll sit down with you, walk through your site, and help build a practical inspection plan that suits your operation. No scare tactics. No jargon for the sake of it. Just honest, hands-on work done properly, with reports you can actually use.
Product Certification ATEX, IECEx, NEC
Our product certification service is a three-step process built to help manufacturers, engineers, and designers get their Ex products into hazardous areas safely and confidently. Whether you're building something brand new or modifying existing equipment for a hazardous area, we’re here to walk the path with you from early concept right through to the final certification. We believe in keeping things straightforward, honest, and practical.
Step 1: Design Review
This is where it all starts — with the drawings, certificates, BOM (Bill of Material), and the concept behind the product. We sit down and look through every part of your design in accordance with the applicable certification scheme you wish to use. Is it fit for purpose? Are the materials appropriate? Which protection method are you aiming to achieve (Ex d, Ex e, Ex i, etc.)? We’ll flag anything that needs changing before you waste time or money building a prototype that is not compliant. And we’re not just here to point out problems! We’ll work with you to find realistic solutions that doesn’t compromise safety or practicality.
Step 2: Inspection & Testing
Once you’ve built the prototype or the final product, we get hands-on. This is where things move from the drawing board to the workshop floor. We carry out physical inspections of the product to make sure it’s been built as per the design, not just what’s on paper, but what’s actually in front of us. This includes completing full detailed inspections, flame paths, gasketing, gland entries, and all the other technical details that matter when certifying something for hazardous areas. We also witness or conduct the relevant testing found necessary during the design review. Thermal testing, ingress protection (IP) testing, dielectric strength, impact testing, whatever the product requires under its protection concept. This stage is where your product proves itself, and we’re there to make sure it does, honestly and fairly.
Step 3: Final Product Certification
If everything adds up — the design is compliant, the build matches the plan, and the test results check out. We’ll give the final thumbs-up to begin the certification process. Once your Final certificate is received, this is your green light to market and install the product in a hazardous area, depending on what scope you're going for. Your product certificate doesn’t just come with a number on it! It comes from our notified body giving you real confidence that the product’s been through a legitimate certification process, that it’s safe, and published with the selected certification scheme. We keep full transparency in everything we do, and we’re always on hand after certification if you need support down the line, updates, modifications, questions from clients, or just peace of mind.
Design Review
Our Design Review Service is where we roll up our sleeves and get right into the guts of your hazardous area design. Not to pick holes, but to make sure it is compliant with the relevant standards and local regulations. Whether you’re working on a brand-new install or modifying an existing one, this review is where we take a proper, clause-by-clause look at your design and see how it stacks up against the standards.
This isn’t a skim read or a surface-level glance. We dig deep. We look at equipment selection and ask: is the equipment selected rated for the zone it’s going into? Investigating the EPL, protection method (Ex d, Ex e, Ex i, Ex n, etc) and is it certified to the correct gas group and temperature class? Are the materials right for the environment? Is the documentation complete and traceable? We don’t make assumptions, we verify. Because when things go wrong in hazardous areas, it’s often because something was missed in the design phase. Our job is to catch those gaps before they become expensive fixes or dangerous oversights.
We also pay close attention to the special conditions of use, the fine print on certificates that often gets overlooked! Things like required clearances, mounting positions, ambient temperature limits, or cable gland types. It’s not enough for equipment to be "certified" — it has to be used the right way, in line with the conditions outlined in the certification. We make sure those conditions are fully understood and accounted for in your design. If they’re not, we’ll flag it clearly, and we’ll work with you to find workable alternatives.
Our design review is based on the actual language of the standards. no guesswork, no interpretations, but line-by-line accountability. We provide clear, structured feedback: what’s compliant, what’s not, and what can be improved. And we explain why, not just because “the standard says so,” but because we want you to understand the logic behind it. That way, you’re not just passing a review, you’re learning how to build better, safer systems for the future.
This service is ideal for engineering teams, project managers, OEMs, or anyone who’s responsible for making sure an installation is compliant before it ever hits the ground. You bring us the design criteria, datasheets, GA drawings, hazardous area classification, equipment lists, and we’ll bring you straight answers, no grey areas!
Hazardous Area Classification Study
At Mantl-Ex, a Hazardous Area Classification Study isn’t something we copy and paste from a textbook, it’s a site-specific work scope that lays the foundation for everything else that follows. If the zoning’s wrong, the equipment won’t be right! If the risks are misunderstood, the safeguards won’t work. That’s why we treat this process with the care and respect it deserves. Not just as a compliance task, but as the backbone of hazardous area safety.
A proper classification study looks at the likelihood and duration of explosive atmospheres forming — whether from flammable gases, vapours, or combustible dusts — and breaks the site down into zones: Zone 0, 1, or 2 for gases, and Zone 20, 21, or 22 for dust. We assess where the potential zones are, how often they’re present, and how far they can realistically spread under both normal and abnormal conditions. This involves more than just glancing at site drawings, it’s about understanding the process, the plant layout, the ventilation, the containment measures, the human factors, and the things that can (and do) go wrong.
We start by walking the site, getting eyes on the actual environment. We talk to the operators, check the process conditions, and look at potential release points. From pumps and flanges to vents and fill points. We consider flash points, Ignition temperatures, release grades, and ventilation rates, and we apply real chemical engineering judgement alongside the standards. Not just what’s written, but what makes sense on your site. Our studies follow international best practices (like IEC 60079-10-1 and 10-2), but we ground them in the realities of your plant, not just the theory.
From there, we map out your hazardous zones with clear drawings, full explanations, and supporting calculations. You’ll get more than just a pretty diagram! We provide justification for every zone, a breakdown of the assumptions made, and clear guidance on what types of equipment are suitable in each area. If you’re dealing with a previous installation, we’ll flag any mismatches between current zoning and existing equipment, and we’ll work with you on a practical plan to bridge that gap.
What sets us apart at Mantl-Ex is that we don’t just drop a report and walk away. We’ll sit down with you, explain the reasoning, and make sure your whole team understands how to apply the classification in real terms. From procurement and design right through to installation and maintenance. If you’ve got contractors or vendors involved, we’ll help them interpret the zones correctly so there’s no confusion or costly mistakes down the line.
A hazardous area classification study is no “walk in the park”. it’s the blueprint for safety and compliance. At Mantl-Ex, we make sure it’s done right, tailored to your site, and delivered with honesty, clarity, and the kind of technical depth that holds up under scrutiny. Because if the zoning’s not solid, nothing else will be!
Hazardous Area Training
At Mantl-Ex, we don’t run a classroom where people sit in silence and click through PowerPoints. We’re not a Comp-Ex or IECEx-certified training provider, and we’re not pretending to be! What we are is a team of people who’ve worked in hazardous areas, hands-on, day in and day out. That’s why we’ve built our own brand of training. In-house, on-site, and straight to the point, focused on what actually matters out in the field.
We call it “Ex-Aware” training because that’s exactly what it is. This is custom-built learning tailored to your work culture, your site, your equipment, and your people. Whether you’re dealing with flammable gases offshore, fine dust in a silo, or old Ex equipment that’s seen better days. We make sure your team understands the risks and knows how to spot issues before they become real problems.
Our training is designed to bridge the gap between compliance and common sense. We take the core principles of ATEX and IECEx, equipment markings, zone awareness, installation do’s and don’ts, inspection basics, and we turn it into understandable context. We talk about what you actually work with. If you’re a maintenance team doing day-to-day repairs, we’ll focus on that. If you’re a supervisor responsible for sign-off, we’ll tailor the content to decision-making and accountability. We’re not here to lecture, we’re here to build confidence and understanding.
This isn’t a tick-box course with a certificate for the wall. It’s proper, face-to-face learning that leaves people with the knowledge and mindset to work safer in hazardous areas, no matter what their role. And because we’re not tied to a rigid syllabus, we can flex the content to suit your team. Toolbox talks, refresher sessions, hands-on walk-throughs, or more structured half-day workshops. We’ll work with you to find the format that fits. Some of our courses can be completed on-line for teams in remote locations, or time sensitive matters.
What We Cover (flexible, not fixed):
· Hazardous area basics (zones, equipment groups, T-ratings, EPLs)
· Understanding Ex markings and certification
· Installation best practices (glands, IP ratings, entries, terminations)
· Inspection types and common faults
· Real-world case studies and what can go wrong
· Human factors and safety culture
· Your site-specific hazards and controls
Whether you're onboarding new staff or refreshing seasoned hands, Mantl-Ex training helps your team understand hazardous areas in a way that sticks. Not just for the sake of compliance, but for the safety of everyone on site. No corporate script. Just honest, boots-on-the-ground training built for your needs.
NOTE: If you are looking for official Comp-Ex or IECEx training courses Mantl-Ex can assist you by referring you to one of our partners within your area of the world.
Digital Solutions
We know that paperwork doesn't keep hazardous areas safe — people do! But we also know that without solid systems behind them, even the best inspectors can get buried in admin and miss what matters. That’s why we’re building Mantl-Ex Digital Solutions. A suite of tools made by people who actually understand hazardous area inspections, because we’ve lived them. Our in-house software will take the hassle out of Ex inspection workflows by giving technicians and duty holders a clear, streamlined way to capture, track, and report on the condition of their Ex-rated equipment right from the field. No more clunky Excel spreadsheets, vague handovers, or backlogged paper reports. This system is being built from the ground up with real-world use in mind: offline functionality, RFID technology, intuitive pass/fail grading, and a full audit trail from inspection to remediation. It’ll be fully aligned with ATEX and IECEx requirements, but flexible enough to suit any site’s unique processes. And just like everything we do at Mantl-Ex, the goal is simple: give you the tools to do the job right, stay compliant, and keep your people safe!
Dossier Creation
We believe in building something that actually means something when you need it. That’s the mindset we bring to our Hazardous Area Dossier (HAD) Creation service. A dossier isn’t just a stack of paperwork gathering dust on a shelf. It’s a living, breathing record of your site’s integrity. It’s your go-to reference when you’re troubleshooting an Ex fault, proving compliance to auditors, or planning a modification. We build dossiers that are clean, complete, and actually usable. Including your hazardous area classification drawings, inspection schedules, equipment certificates, installation specs, repair records, and everything else the standards ask for. We don’t just copy and paste; we dig in, verify what's missing, and help you pull it all together, even if you're starting from scratch or trying to untangle years of patchwork documentation. Whether it's ATEX or IECEx we align it with the standards, but explain it in plain language so you and your team know where everything stands. Because when something goes wrong, the last thing you want is to be flipping through folders in a panic. You want to know that your Ex documentation is solid, structured, and easy to navigate.
Contact us
Need clarity on your compliance? Start the conversation with Mantl-Ex today